2007-04-05 18:12:57 UTC
- Nuova Simonelli Mac Digit Manualminerenew Numbers
- Nuova Simonelli Mac Digit Manualminerenew 0
- Nuova Simonelli Mac 2000
- Nuova Simonelli Mac 2000v
- Nuova Simonelli Mac Digit
Nuova Simonelli Mac Digit Manual 10 No profanity, illegal acts or personal attacks will be tolerated in these discussion boards. No commercial posting of any nature will be tolerated; only private sales by private individuals, in the 'Buy and Sell' forum. No SEO style postings will be tolerated. SEO related posts will result in immediate ban from CoffeeGeek. Thoroughly cleaning your commercial espresso machine regularly (at least daily, but sometimes throughout the day if your cafe is busy enough) will increase i.
- Nuova Simonelli is an Italian company with experience and tradition going back many years. It has been making espresso machines, which it exports all over the world, since 1936. One more honor that Nuova Simonelli enjoys is being an official machine sponsor at world Barista Championship after passing a rigorous testing phase.
- Fits to models Appia Compact, Appia, Aurelia, Master Coffee, Premier MAXI, Mac 2000 1 Group, Mac 2000 2 Group, Mac 2000 3 Group Add to cart Nuova Simonelli Parts.
- Cafelat Silicone gasket 8.3mm NS, 71 mm x 56.5 mm x 8.3 mm (Red) conical, for all of the older models of Nuova Simonelli, including the Program, Optima, Personal, Program VIP, Premier, Premier Maxi, Mac Digit, Mac Cup, Mac 2000, Oscar, Oscar II, Musica, Appia and Appia I.
Personal, I thought this would be a good time to back off & encapsulate what
I've done & the lessons I've learned. This is NOT a solicitation to sell
this machine, but an effort to pass along some hard-learned knowledge to
anyone contemplating such a project.
First, let me acknowledge the good folks here in alt.coffee & Coffee Geek.
The advice & help so generously provided was of enormous (indispensable?)
help. I won't bother naming names - you know who you are & I want to just
say that without you folks these groups would devolve into quickly oblivion.
THANK YOU, ONE & ALL!
I rebuilt the Mac for a friend who, when the job was finished, told me that
his spouse didn't want the *thing* in her kitchen. He suggested a swap for
an extra Mazzer grinder I had, so now I own this machine.
Nuova Simonelli Mac Digit Manualminerenew Numbers
In the rebuild process I started from a knowledge base of near-zero. I'dreplaced rotary pumps, gaskets & a few other parts for friends with
commercial machines. But this was to be my first *frame off* restoration of
a professional espresso machine. Not easily daunted, I plunged recklessly
into the project; as they used to say in the Army of the uniniated, 'Fat,
dumb, & happy'.
First I had to figure out how to get the exterior panels off. Neither the
owner's manual or the parts manual gave up any clues, so I begged for help
in alt.coffee & thankfully someone shared their knowledge. By removing four
Allen bolts under the top cover & two long-headed (what else can you call
them?) hex head bolts under the drip tray, the two side panels can be slid
forward & off. The back panel required the removal of four bolts hidden
behind the frame on either side of the boiler.The front panel removal
required that the Inox panel surrounding the group be first removed. Loosen
the two Phillips screws inside the panel that hold it to the front panel &
remove the other screw that connects it to the underside of the control
panel. Pulling open the ends of the panel frees it from the two loosened
screws & it lifts out. Remove the four Phillips screws holding the front
panel to the frame & lift it out.
Once exposed the internals of the machine were open to inspection & easily
accessed for repair. Here's where I used Paul Pratt's advice & started
taking pictures of everything, from all angles. I then started removing the
copper tubing & fittings. The boiler & group came out easily enough after a
bit of head scratching & more than a few 'Hail Mary's'.
At this time let me point out that before the acidic bath each part is
soaked in a hot bath of industrial strength caustic detergent (otherwise the
acid bath would be less effective). I have a heated tank used to degrease
engine parts that agitates the solutions used around the parts. This is a
tools not available to most enthusiasts, but if you strike up a good
relation with *friendly* independent mechanics or parts store clerks you
should be able to find one you can use.
I pulled the element from the boiler & dropped it & the boiler into the
tanks of hot solution. The boiler was in pretty good shape externally with
the nickel plating intact & corrosion minimally present. Internal inspection
revealed slight scaling & a discomforting(!) wear spot on the HX tube. I
don't know if the element is coming into contact with the tube or if the
wear spot is due to the close proximity of the HX to the heat source? I
decided to alter the element's shape a bit to provide extra clearance just
to be on the safe side. Once it's reassembled, I suppose the only way I'll
know if there's a problem is when the HX ruptures & water starts flowing
from the group when the pump is off?
The group was soaked in the detergent bath only & all fittings were removed.
While it was submerged, I ran a tube-brush, connected to a pneumatic wrench,
through all of the passages. After this loving attention the group came out
spiffed up (technical jargon) & like-new.
For the copper tubing I jury-rigged a device that, at the risk of sounding
less than humble, I like to think of as truly inspired. The copper tubing is
connected using rubber surgical tubing to an Ulka pump. The pump's intake
Nylon tube & the output from the copper tubing was submerged in a pot of
acidic solution kept at 95 degree Fahrenheit. This recalculating warm

badly scaled tubes to a gleaming like-new finish. (I was sorely tempted to
trash the copper tubing & replace it with high-temp Nylon tubing. But, since
this was not my machine at the time I opted to clean the copper instead.)
When inspecting the machine prior to pulling it apart I saw a bit of rust &
corrosion under the pump. After disassembly I found the 'T' fitting for the
outlet side of the pump was cracked. Other than it's replacement all other
hard-parts (S/S, copper, brass) were reusable after cleaning. I did opt for
new o-rings & gaskets & where I couldn't find the correct size or materials
I opted for the ol' standby - Permatex RTV (NSF certified) sealant. This
stuff is a must for anyone working with hi-temp water/steam systems - it &
the other great standby, JB Weld, have saved me many times when a project
was dead-ended because of an unobtainable of broken part. If you don't have
these in your toolbox, RUN to the hardware store now 7 get some, because
eventually everyone will need one or the other in a *hurry*.
Thanks to the many pictures I took, reassembly went off relatively smoothly.
Fittings were tightened, wires were connected, & the water & drain lines
were connected. I turned the water on & filled the boiler after getting help
figuring out that the pump has an auto shut off if it runs for too long.
Powering the machine on & off until the boiler filled solved this issue.
With just the mains pressure I let the machine sit powered on for 30 minutes
to achieve a stable boiler temp. I checked for & found the expected small
leaks. One o-ring was cut installing it (simple replacement fixed it), but
everything else just needed to be tightened a bit to stop the leaks. I let
it set the rest of the day without running the pump just to be safe, without
finding more leaks. Yeah!
I then began adjusting the pstat & pump pressures. I set the pstat to 1.2
Bar & the pump to a bit under 9 Bar (both based on empirical testing, using
myself as the willing guinea pig). Using week old beans I eventually began
pulling shots that were almost exclusively crema. Happy, Happy, Happpy!
The exceptions to the easy reassembly were the plastic side & back panels.
The mounting bolts screw into brass lugs that are pressed into holes formed
in the plastic panel. Probably due to being dropped at some point, several
of the lugs had been broken out of their holes (in fact this probably
explains the cracked 'T' fitting mentioned above). Aha, yet another job for
JB Weld! After fixing this problem everything went together quickly.
Boy, did this machine look good. If I didn't already have the Bunn ES-1A
that I've grown to love dearly, I might have opted to use this machine for
myself. That plus the plastic panels being a *very* boring charcoal grey
Nuova Simonelli Mac Digit Manualminerenew 0
made me decide to keep the Bunn & sell the Mac.
There were many times I had to come back to the groups, sometimes for
critical help & even more often for simple hand-holding reassurances. I
could have successfully completed this project without this advice (the
machine is way too simple to be *much* of a problem to figure out) but I
Nuova Simonelli Mac 2000
Nuova Simonelli Mac 2000v
would have made costly mistakes in doing it on my own, so once again I sayTHANK YOU to everyone that helped me in this project.
Nuova Simonelli Mac Digit
--
Robert (Gig 'em!) Harmon
www.tinyurl.com/34r5dx - My attempt at blogging.
www.tinyurl.com/2tnv87 - Guidelines for coffee newbies.
www.tinyurl.com/37gwfr - I have stuff available for sale.
Robert (Gig 'em!) Harmon
www.tinyurl.com/34r5dx - My attempt at blogging.
www.tinyurl.com/2tnv87 - Guidelines for coffee newbies.
www.tinyurl.com/37gwfr - I have stuff available for sale.
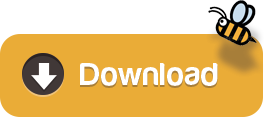